VMC1160 Vertical Machining Center
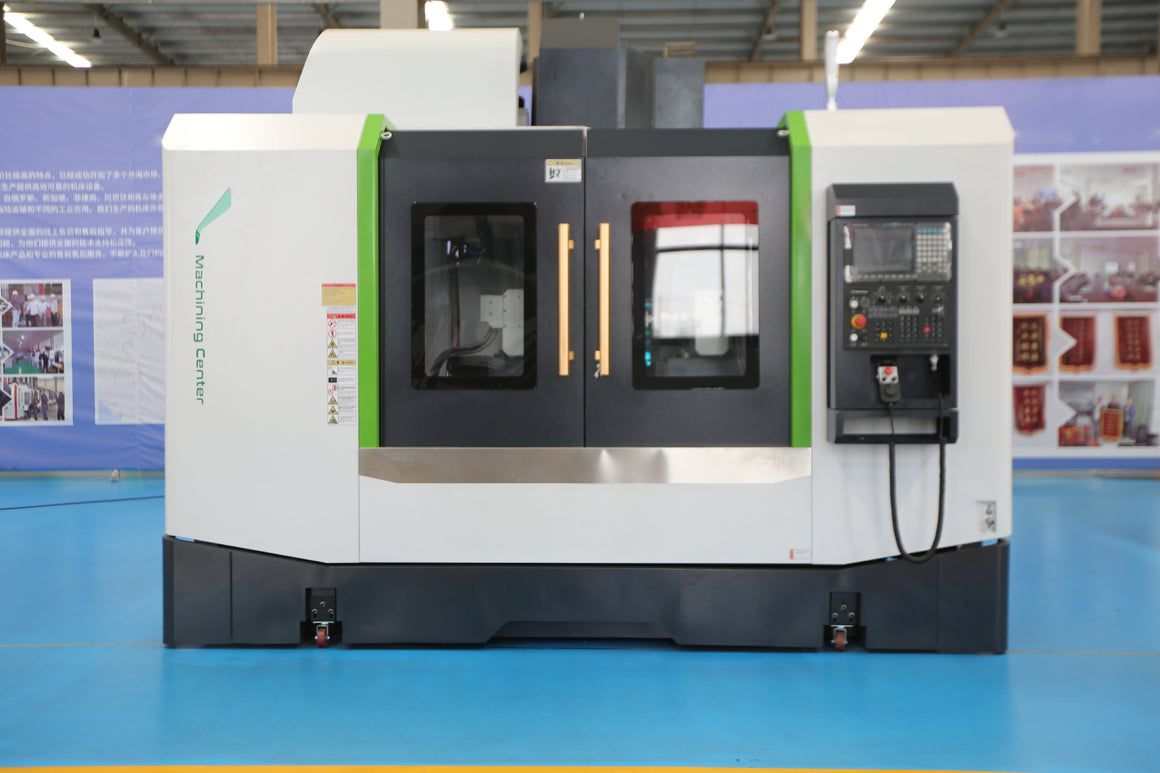
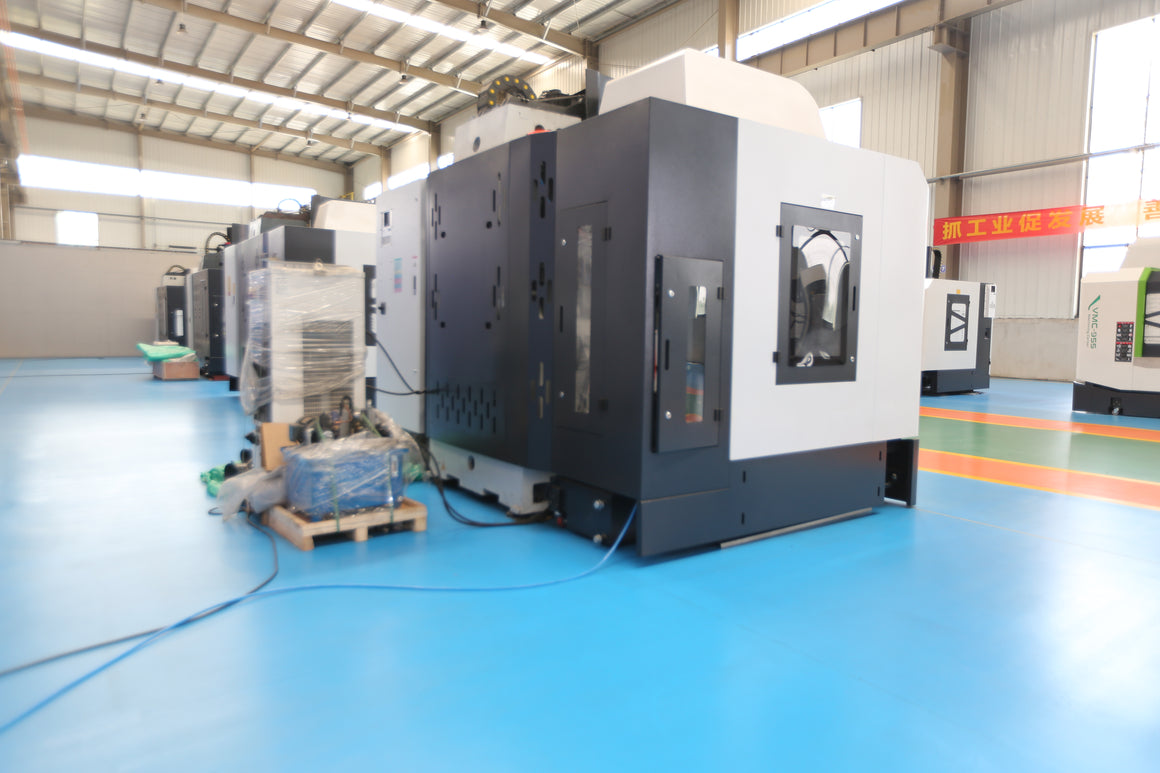
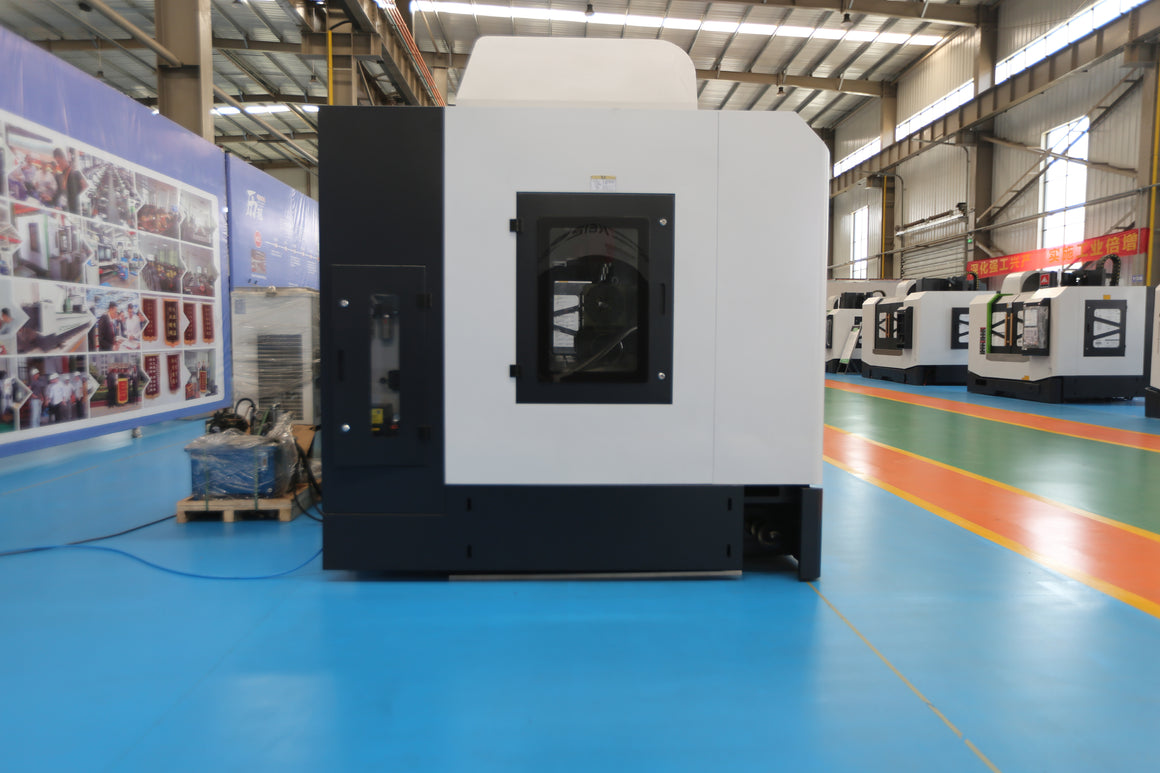



Couldn't load pickup availability
Vertical machining center VMC series
The machining center is mainly suitable for machining workpieces with complex shapes, multiple processes and relatively high precision requirements.
1. Box-type workpieces This type of workpiece generally requires multi-station hole system and plane processing, and has high positioning accuracy requirements. When processing on the machining center, one clamping can complete 60%~95% of the process content of ordinary machine tools. 2. Complex curved surface workpieces Complex curved surfaces can generally be processed with a ball-end milling cutter for three-axis linkage machining with high machining accuracy, but low efficiency. If the workpiece has a machining intervention area or a machining blind area, it is necessary to consider using a four-axis or five-axis linkage machine tool. Such as the appearance of aircraft and automobiles, impellers, propellers, various molding molds, etc. 3. Special-shaped parts Special-shaped parts are irregular parts, most of which require point, line, and surface multi-station mixed processing. When processing special-shaped parts, the more complex the shape and the higher the precision requirements, the more superior the use of a machining center can show its superiority. Such as mobile phone shells, etc. 4. Disc, sleeve, plate workpieces This type of workpiece includes disc sleeves or shaft workpieces with keyways and radial holes, and end faces with hole systems and curved surfaces, such as sleeves with flanges, shaft parts with keyways or square heads, etc.; plate parts with more holes, such as various motor covers, etc.
Machine tool configuration
1. The machine tool body adopts an original three-dimensional variable diameter structure design. After finite element analysis, the body structure is optimized to the greatest extent, ensuring the stability and reliability of the body, and preventing the body from deformation, thereby increasing the service life of the machine tool.
2. The machine tool slide adopts a box-type design, and the dense reinforcement ribs inside the box are arranged, which doubles the accuracy of the machine tool.
3. The machine tool column adopts our original "humpback" design, which effectively prevents the body deformation problem and greatly enhances the rigidity of the spindle at the high point position.
4. The machine tool worktable adopts a double-layer reinforced design. The increase in the thickness of the worktable effectively hides the interference of the installation of the linear guide slide on the worktable, further enhancing the rigidity.
5. The X\Y\Z axis guide rails of the machine tool all adopt a large span ratio, which increases the weight of the machine tool as a whole, thereby improving the stability of the machine tool.
6. The ball screw nut of the machine tool is an extended design, and the preload force of the nut has been effectively improved, greatly extending the service life and precision retention of the machine tool.
7. The ball screw of the machine tool adopts a pre-matched locking nut structure to effectively prevent the locking nut from loosening.
8. The machine tool adopts our original active lubrication system, and the oil pump is directly controlled by the CNC system to discharge oil, which truly achieves on-demand oiling, and can sense the problems caused by the machine tool oil circuit to promptly warn customers to prevent damage to the machine tool.
9. The machine tool adopts a support-type pulley block internal protection design, so that the internal protection is always parallel to the guide rail during movement, and is not easy to deform, which improves waterproofness and extends service life.
10. Each machine tool must be accurately matched with the weight of the Z-axis counterweight according to the customer's purpose. The machine tool is optimized according to the products produced by the customer.
Main Technical Parameters | VMC1160 |
X,Z Axis Travel | 1100mm*600mm*600mm |
Distance From Spindle Center To Z-Axis Guideway Surface | 675mm |
Distance From Spindle End Face To Table Surface | 120-720mm |
Table Size | 1200*600mm |
Cutting Feed Speed | 1-10000mm/min |
Rapid Traverse Speed | 24/24/24m/min |
Maximum Table Load | 900kg |
T-Slots (Number X Width X Spacing) | 5mm*18mm*120mm |
Spindle Speed | 50-8000rpm |
Spindle Taper Hole | BT40-150 |
Spindle Power | 11/15kW |
Servo Motor | βis22/3000 |
Tool Magazine Capacity | 24Handles |
CNC System | Fanuc/Siemens/Mitsubishi/Syntec/Knd |
Positioning Accuracy | 300/±0.005mm |
Repeat Positioning Accuracy | 300/±0.003mm |
Air Source Pressure | 0.6MPa |
Electrical Capacity | 25-30kW |
Machine Dimensions | 3400mm*2420mm*2600mm |
Machine Weight | 7.6t |